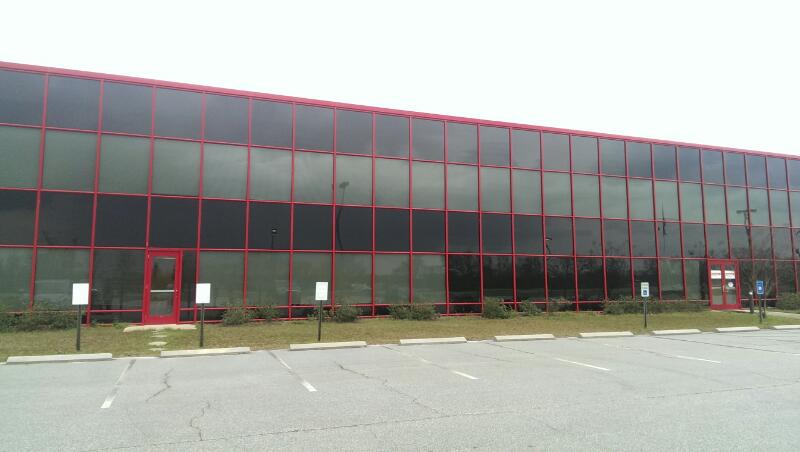

Photo courtesy of Office of the Governor/Andrea Briscoe
Bainbridge Manufacturing, which will make air conditioning parts for automobiles and other industries, was welcomed to Bainbridge by Georgia Governor Nathan Deal in November 2013. The company was originally slated to get started in 2014 but is still in pre-production.
That delay has caused some anxiety among local leaders, who are anticipating Bainbridge Manufacturing’s impact on the local job market and economy. However, Abraham Levy, the CEO of Bainbridge Manufacturing answered many of the questions local leaders had about the factory’s opening during a recent tour of the company’s plant, located in the Decatur County Industrial Air Park, off U.S. 27 North.
Joining Abraham Levy was his father, Liliem Levy, who is the president and founder of Global Air Inc. of Miami, Fla., the company which will transition its work into Bainbridge Manufacturing. Also present was Paul Merkt, a young engineer who has been working at the plant’s office for several months. Merkt designs many of the blueprints used in the company’s manufacturing process.
One of the main messages that came out of the tour was that Bainbridge Manufacturing has had to overcome several unforeseeable issues with its building, formerly occupied by TRACO from 2006-2009. The building, formerly a spec industrial building, is 177,970 square feet on 27.89 acres.
TRACO spent a lot of money on refitting the spec building for its own needs, and at one point employed up to 200 people. However, TRACO’s decision to lease its vacant building out for peanut storage in 2012 seems detrimental in hindsight.
While huge mounds of peanuts were being stored in the building, field mice and rats ate their way through the building’s roof and destroyed the insulation in its ceiling and walls. The mice also chewed through Internet cables and electrical wiring.
The mice also left behind waste and caused other damage to the building as they created entry and exits within the plant. Even on Thursday, Levy pointed out places where peanut shells were recently discarded by mice and fell from the ceiling to the factory floor.
Bainbridge Manufacturing has contracted with a local pest control company and has done much cleanup, but there is still significant repair work to be done to fix what the mice damaged.
Bainbridge Manufacturing also had to make a significant investment of its own to re-supply its warehouse with electricity. The Development Authority of Decatur County helped with pouring sturdy concrete back into gaps in the factory floor that were caused by TRACO machinery being removed.
Bainbridge Manufacturing has also had some issues laying down a test section of a new factory floor. The company has reason to believe that the issues are possibly caused by peanut oils having seeped into the concrete subsurface. Another theory is exposure to ultraviolet light streaming in from roof skylights.
Bainbridge’s Jim Overman, who works with Big Bend Industrial and other firms, is one of several consultants testing possible solutions to why the test floor section has experienced discoloring.
After the mice ate through the roof insulation, rain water leaked down onto the concrete floor and pooled, leaving behind rust spots.
Abraham Levy said his overall goal is to create and maintain a very clean, efficient working environment that not only boosts employee morale but also could impress the company’s future clients. He described details of a specific vision for what the factory floor will be like once workers are in place, and said his inspiration came from European automotive plants which take pride in their cleanliness.

What exactly will Bainbridge Manufacturing produce? The company’s predecessor, Global Air, is primarily known for manufacturing aftermarket heating and air components for automobiles, including radiators, condensors, or evaporators. “Aftermarket” means the company makes parts that are not from the original manufacturer, but are otherwise compatible. They are usually less expensive but are still quality products. If you took your car to the repair shop and the mechanic had to replace your vehicle’s radiator, he could choose to install an aftermarket part to save money and/or time.
However, Levy made it clear that Bainbridge Manufacturing is not limiting itself to any niche industry and has invested in the factory equipment it could use to produce parts for a number of industries.
Anything that requires a process known as extrusion, could be made by Bainbridge Manufacturing’s assembly line, after a future expansion is complete. One example is metal window frames.
Extrude – to form (metal, plastic, etc.) with a desired cross section by forcing it through a die. (Random House Dictionary)
Levy described the general process by which Bainbridge Manufacturing takes original manufacturer parts and reverse-engineers them using 3D modeling software and blueprints. The reverse-engineering is done primarily by engineer Paul Merkt, but Levy said he was hopeful to partner with local educators and students to teach the necessary skills.
“We need to make blueprints for over 12,000 products,” Levy said. “It’s a very precise, time-consuming process. Without the drawings, we won’t be able to make the parts.”
Levy said the 3D modeling/rendering process alone could employ 10-15 young people or adults, once they learn the requisite skills in CAD (computer-aided drawing). He said the company has plans to provide training to interested computer-savvy individuals, and teach them to “speak the language of blueprints” that are used in manufacturing.
“That is the most critical position that we need to fill immediately,” said Levy, who hopes to conduct training sessions this summer.
Levy said he has experience in the automotive and aeronautical manufacturing industries, and Merkt and Liliem Levy also come from automotive manufacturing.
“I know people have said, ‘you haven’t created jobs yet,’ and that’s true,” Levy said. “But everywhere we can, we use local companies to help us with whatever we need to do in the building.”
Those local companies have done work in the areas of flooring, concrete, Internet, heating and air and pest control. Levy said he’s also working with a local realtor on finding him a home in Bainbridge.
Bainbridge Manufacturing has shipped most of the equipment from Global Air’s plant in Miami Gardens, Fla., where light manufacturing is still going on, to Bainbridge. Large pallets of factory machinery components could be seen on the tour. The components are wrapped up in black plastic, to keep dust and pests out until they can be put together.

More machinery will be arriving over the next three months, and the last piece should arrive in June. Levy said he planned to hire 3-5 workers in March; he said that for the first month, they would help do maintenance and cleaning (including pressure washing) of the factory’s surfaces, which still have peanut dust on them. After that, they will begin unwrapping some of the machinery components and putting them together.
One of those machines is a large furnace that will be used to heat up pieces of aluminum metal used in Bainbridge Manufacturing’s products, that are then welded together. The furnace was made-to-order in Europe, and was so large that the company that made it had to expand its facility before producing it, which also caused a delay. Even now that it’s arrived, the furnance will take about 1.5 months to put together.
However, Levy said the large furnace will be a major competitive advantage for Bainbridge Manufacturing and allow it to get into other product markets at a later date, if it chooses. The company also has experience using robots to assemble parts; those robots are programmed by humans for specific tasks, according to the blueprint for a product.
“That doesn’t mean there will be no production until June,” Levy said. “We’re going to be making the components to make the evaporators and condensors. We’re going to be training people on milling, lathes and welding, so that when we launch into production, it will be easy for them to program the machines and use them.”
Workers can also get started on a contract the company has to make bent tubing for air conditioning systems, which doesn’t require the furnace.
After the initial 3-5 hires in March, Levy said he expects to hire 6-8 more people in April.
Bainbridge Manufacturing has hundreds of resumes that have already been sent to it; if you are interested in working for the company, contact the Georgia Department of Labor’s office on Scott Street in Bainbridge online or by calling (229) 246-2618.
Full-scale production with the first shift will come in August, Levy predicted. He said that would be about 30 people.
“We will start with one shift, then add a second 2-3 months later. By the end of 2015, we hope to be at full production with three shifts.”
Levy pointed out that part of Bainbridge Manufacturing’s commitment is to create 80-100 jobs by the end of its third year of production.
“That’s the commitment, that’s the promise, that’s what we will do,” Levy said.
By the end of year 10, the commitment will be up to 250 jobs, which will come from the two factory expansions Bainbridge Manufacturing has plans for.
“It’s important for us to hire the adult population, but we have to think long-term about who will be filling these jobs 10 years from now. If we don’t start exposing people to manufacturing, we’re going to have a tough time expanding in the future.”

Although the use of robots somewhat reduces the total number of needed workers, Levy said the goal is to use robots to perform the repetitive tasks and leave humans to focus on tasks that require analysis and other higher-level thinking. That speeds up the manufacturing process and makes it cost-competitive with Asian manufacturers, who are still relying on cheap labor.
“We’re not going to be hiring people that do things like, ‘put one part in, take another part out. We’re going to teach people how to program these machines and how to program the robots.”
The company has plans to expand its current warehouse both to the rear and to the side. The extrusion assembly line will be more than 1,800 feet long, stretching across what is currently a grassy field along Industrial Boulevard.
Bainbridge Manufacturing will have a major need for natural gas to continually run its furnace (it will take three days to start it up initially). The company will look to save money on shipping by producing raw materials itself, and heating will be part of that process, Levy said. Decatur County Commissioners are finishing up installation of a new six-inch natural gas line that will serve expanded needs of customers at the Industrial Park, including Bainbridge Manufacturing.
Levy described how he and his father chose Bainbridge for the site of their new company. (Working with the Georgia Department of Economic Development, the Levys also looked closely at Dublin, Ga., before deciding upon Bainbridge). The senior Levy had expressed interest in retiring, and asked Abraham to consider taking over for him. Only, as it turns out, Dad isn’t retiring just yet and is helping his son with the transition from Global Air, in Miami, Fla., to Bainbridge Manufacturing, in Georgia.
Levy said he believes Southwest Georgia has a good workforce for manufacturing and Bainbridge also had a building that was large enough and in comparatively good shape in the former TRACO building. Bainbridge is also located relatively close by rail and truck to the Port of Savannah, Ga., which is the second-largest port in the United States. The port of Savannah’s position on the Atlantic Ocean will also be key as Bainbridge Manufacturing ships its products to European and South American customers; the shipping time from Savannah to Europe is much faster than shipping from China, Levy said.
Levy, who is an American citizen, expressed pride in knowing that the products will bear the “Made in the USA” logo. He said not only do American products rightfully have a reputation for quality, because of our manufacturing and labor standards, but there’s also an economic incentive: the company will gain manufacturing partners and end-users who are willing to pay for American quality; and in return, Bainbridge Manufacturing’s future success could benefit Bainbridge and Decatur County and its citizens.
Be the first to comment